Just received this update from Odyssey.
A noticed a reference to an Aussi buyer. Is this your bench, @tompoland 😁

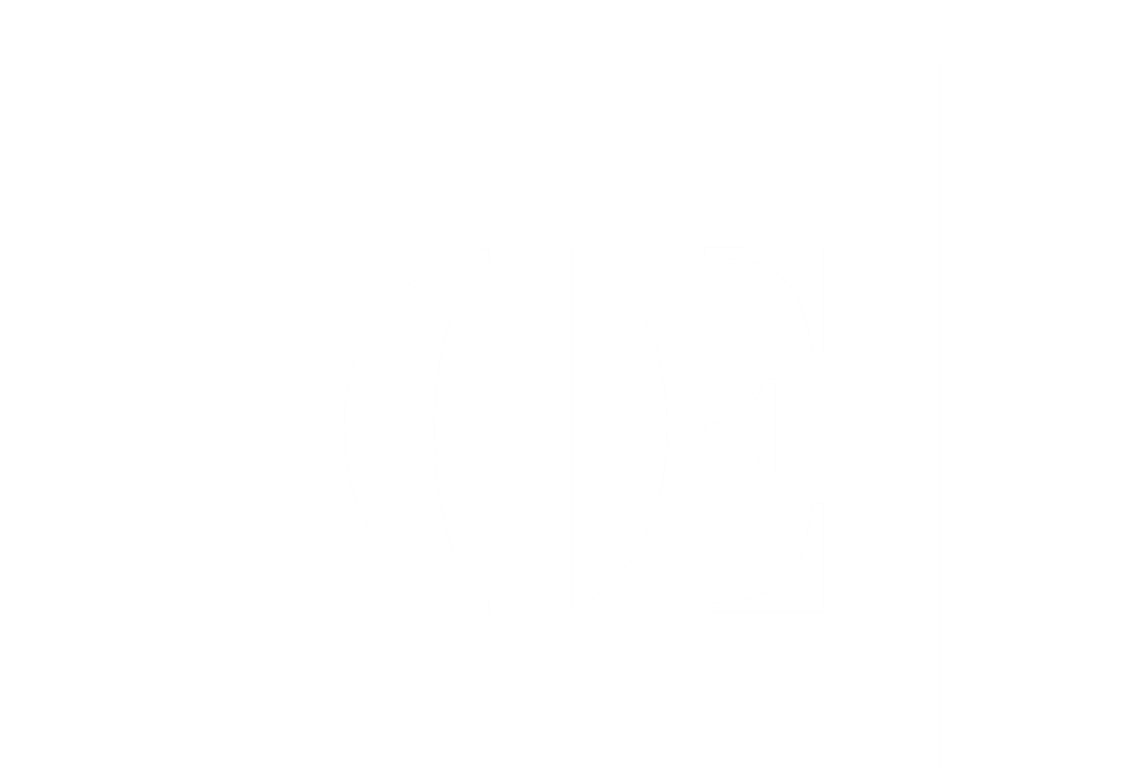
Odyssey Espresso Argos Update: August 1, 2023
Hello All,
We’ve gotten behind on updates but wanted to start by saying despite the delays, there are no serious issues. We’re just trying to figure this whole hand built small batch production thing out.
Quality Control Bottleneck
The last few weeks of assembly have not been going as smoothly as hoped. Our original quality control procedure involved pulling 4 shots through the Scace unit to verify output temperature was matching the brew set temperature within our expected tolerances. We found that all of the machines that were operating correctly were staying within our 2C tolerance band. The bigger issue we ran into was machines being built incorrectly and having miscellaneous fit or function problems. Those machines had to go back to the build process to be torn apart, corrected, and re-tested.
This took time to not only figure out how we could modify our assembly process for better success but also modify our QC process to focus more on longevity instead of a single set of shot pulls. We have also modified our assembly procedure to now require each tech to perform an initial test run after they build each machine. If any issue arises, that particular technician will then be able to see the problem and fix it immediately before continuing on to the next build. This previously created a bottleneck for us where a technician would continue building machines that were failing QC then being sent back to rework which prevented us from actually shipping any units out. Our current goal is to have a completely finished and QC’d machine packaged up and ready to ship before a technician can continue on to the next.
Technician Assembly
We’re still working on hiring more technicians. Unfortunately we are now down to 2 technicians. We’re very happy with the work that these two are putting out and look forward to continuing to grow our team. We know attention to detail is a must for this role and are still refining our interview process to find technicians that are most likely to succeed in this environment.
Resolving Issues
After we sent the initial machines out, we came across a few cases with grounding issues. We’ve since found solutions for all of those which included adding washers to space our PCBs off from the mounting plate more and ensuring that the electrically resistive tape between the PCB and mounting plate fully covers all solder points on the back of the board.
Updated Quality Control Process
We have an ever evolving QC process. As we continue to build and test we find new things to add to the list to improve quality and consistency. We’ve started blowing out any residual water from the fill tube and steam wand lines before shipping. This is a simple process but adds an additional step that we think is necessary for general product cleanliness.
General
Due to the dynamic nature of a small shop startup we will always continue to try things out, learn, and adapt. We thought that a Launch Checklist with an Order Progress Log would be helpful for customers to track orders as they’re built, QC’d, and shipped out. Unfortunately because we’ve had optimistic projections on our build efficiency and been wrong, we’ve decided to remove this progress log and include what’s been shipped out in our newsletter updates. This way we avoid giving false hope and can aim to do a better job at keeping people up to date with actual progress.
We know people will continue to ask and make assumptions about when their orders will ship but there is realistically no way to know this information. We have proven that at our current stage, nothing is consistent from week to week in the current build process. We will continue to improve our efficiency and build as many machines as possible but there’s no way to know when exactly you’ll hire new shop techs or lose some. We’re working to make things stable so that projections can be made but cannot promise when that will happen.
We currently have 8 machines in boxes that have been QC’d multiple times due to our changing and added processes. The only thing left for these machines is the shipping label and dropping them off at FedEx.
9 more machines need the final stage of water blown out of the lines then are ready to go into boxes.
Our two shop techs will be back to building new machines this week.
Ross is taking some time off from his day job to focus on getting the shop organized and working with our techs to implement a streamlined method of going from build all the way to packaged and ready to ship before moving on to the next machine.
Videos
A video showing how to swap between springs and from spring to direct has been filmed and is being edited for YouTube.
A video showing how to install the analog pressure gauge, transducer, or both has also been filmed.